Insights What's next for the USA's prefabricated building market?
“Modular construction”, the creation of either permanent or relocatable modular buildings, is expected to grow by 50% by 2028 according to a recent study. This study, extrapolating from current developments and adjusting for the impact of the pandemic, considers modular construction to be every type of factory-constructed building, also called componentry. The market includes not only permanent or relocatable, but also residential, commercial, industrial and specialist buildings.
The global construction market is projected to grow by $9 trillion by 2030, with China, India and the USA as the major players. Given that China’s construction sector is also projected to drop to an unprecedented low, this puts American companies and their personnel at the forefront of developing new materials, techniques and processes to build safely and sustainably. Engineers and construction managers will be pioneering technology and systems to help America meet this need in the domestic market as well as supporting construction in complex and often challenging environments.
Modular buildings - home in a box?
Prefabricated housing is key to building affordable housing in remote areas because although prefabricated buildings are not necessarily that much cheaper than traditional structures, they generally deliver much lower time and labor costs onsite. This is being recognized in Colorado, where the state legislature is debating a bipartisan proposal to create a $40 million fund to support “innovative” housing manufacturers to help close a 127,000 housing gap shortage. Other states that might benefit include California which was reported to have a 978,000 housing underproduction in 2019 and Texas with a 322,000 shortfall. These states also have large rural areas where construction access can be demanding but the opportunity to improve local economies is great.
The growing prefabricated market is just another signal that the US construction market is by no means staying still. It’s an industry that will continue to change the way we live for the better, thanks to the work of innovative engineers, project managers and other skilled professionals. Professionals. At AtkinsRéalis , and within our brands Atkins and Faithful+Gould, we aim to lead the growth of the US construction market. With our well-established expertise in engineering and our innovative approach - such as using data to support sustainable, cost-effective building programs – we believe we have the perfect mix to make this happen.
Innovation, sustainability and prefabricated buildings
One rapidly developing area of modular construction is automation. Prefabricated buildings combine the potential to work with sustainable design and verified supply chains to ensure that buildings are both environmentally friendly and efficiently produced. Fully automated factories creating modular building systems already exist in the USA, but the next stage of this process is to create as much of a circular built economy as possible around prefabricated buildings. The gains here are evident, not just in sustainable material use, but also the benefits from using data to support decision-making, novel engineering approaches to reduce climate impact and imaginative design to increase the life-span of components.
There are two major ways that prefabricated buildings can improve sustainability:
1. Repurposing and recycling prefabricated building elements back into the manufacturing process
2. Re-using and/or re-siting prefabricated buildings to prolong useful life
These two routes are not mutually exclusive. For example, in a recent article on hotel construction, a variety of opportunities are mentioned, from using old tires to create tiling, to using modular construction to build hotel structures, which could later be re-sited for prefabricated office use. Additionally, cross-laminated timber—which was incorporated into the 2015 International Building Code—can be prefabricated and then repurposed into the circular building environment. On a global level, Atkins focuses on circular built environments as part of the Race To Zero and is a major contributor to implementing forms of circular design, construction and repurposing to achieve sustainability goals.
Help create a sustainable future at Atkins
At Atkins, we’re focused on a more sustainable built environment. We create and deliver innovative solutions around the world, and we’re at our best when combining new technologies with forward-thinking. If you’re looking for the kind of challenge that makes the world a better place, and you’re ready to engage with some of the most exciting construction management jobs, why not browse our available vacancies in the USA?
Interested? Find out more about life at AtkinsRéalis
Sign up to receive the latest content tailored to your interests
Our articles

Preview
Middle EastContent type
BlogsPublish date
04/26/2024
Summary
By implementing reforms in the public sector and wider society, the KSA’s Vision 2030 has greatly improved government efficiency, bringing about new growth and investment opportunities. What is Visio
.jpg)
Preview
IndiaContent type
BlogsPublish date
04/25/2024
Summary
In the ever-evolving landscape of professional endeavours, finding a workplace that feels like your safe space is a rare gem. AtkinsRealis stands as a beacon in this regard, where talents not only
.jpg)
Preview
IndiaContent type
BlogsPublish date
04/25/2024
Summary
In the ever-evolving landscape of urban drainage modelling, AtkinsRéalis stands as the leaders with large highly skilled urban drainage modellers. Our focus on serving our clients around urban dra

Preview
CanadaContent type
BlogsPublish date
04/25/2024
Summary
Since the start of the COVID-19 pandemic, the skill of managing constantly changing environments has become more and more important. New construction project management software offers innovativ
+(1).jpg)
Preview
AustraliaContent type
BlogsPublish date
04/24/2024
Summary
In a momentous shift, SNC-Lavalin has transitioned to AtkinsRéalis, marking a new era of innovation, collaboration, and excellence in engineering consultancy. With this rebrand comes a fresh persp
.jpg)
Preview
IndiaContent type
BlogsPublish date
04/23/2024
Summary
As Mumbai continues to evolve and expand, the demand for sustainable infrastructure and cutting-edge technology has never been more pressing. At the forefront of this transformative journey is Atk

Preview
EuropeContent type
BlogsPublish date
04/22/2024
Summary
Hi there! I'm Paul, a civil engineer with over 25 years of experience specializing in networks and drainage engineering. My role at AtkinsRéalis spans managing projects, directing major initia
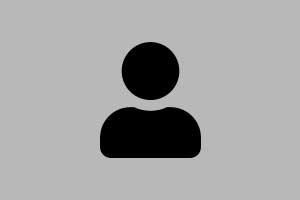
by
Shailaja Mantha

Preview
EuropeContent type
BlogsPublish date
04/22/2024
Summary
Meet Paul, a talented civil engineer in water management whose career journey is as inspiring as impressive. Starting at AtkinsRéalis, fresh out of university in 1997, Paul quickly distinguish
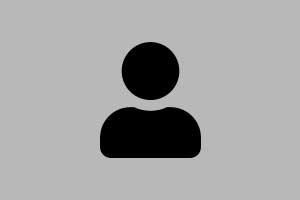
by
Shailaja Mantha

Preview
Middle EastContent type
BlogsPublish date
04/18/2024
Summary
In the vast expanse of the Saudi Arabian landscape, you’ll find a beacon of innovation, a vision for a better, greener tomorrow. NEOM sits in the heart of the Tabuk province and isn’t just anothe

Preview
AsiaContent type
BlogsPublish date
04/18/2024
Summary
As a global metropolis, Hong Kong has long been a fantastic place to be a civil engineer. With world-class infrastructure all around, effective civil engineers have many opportunities to be a
.jpg)
Preview
AustraliaContent type
BlogsPublish date
04/18/2024
Summary
In January 2024, Srijana embarked on a new chapter in her engineering career, joining AtkinsRealis as a Chartered Structural Engineer. With six years of experience on a wide variety of projects, Sr

Preview
EuropeContent type
BlogsPublish date
04/17/2024
Summary
I'm Dean, Regional Director at AtkinsRéalis since July 2023. I'm a Chartered Quantity Surveyor in the Projects & Programme Services team with director-level experience across various sectors,
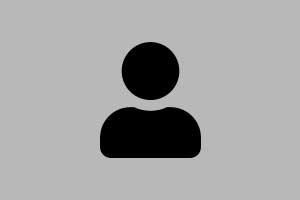
by
Shailaja Mantha
AtkinsRéalis
Equality, diversity and inclusion
We’re devoted to growing the diversity of our people, promoting an inclusive culture, providing everyone with an equal voice because simply put, it’s the right thing to do. Click to learn more.
Find out more